Porosity in Welding: Identifying Common Issues and Implementing Finest Practices for Avoidance
Porosity in welding is a prevalent issue that frequently goes undetected until it creates considerable issues with the stability of welds. In this discussion, we will explore the key variables contributing to porosity formation, examine its harmful impacts on weld performance, and review the ideal techniques that can be taken on to reduce porosity incident in welding procedures.
Common Root Causes Of Porosity
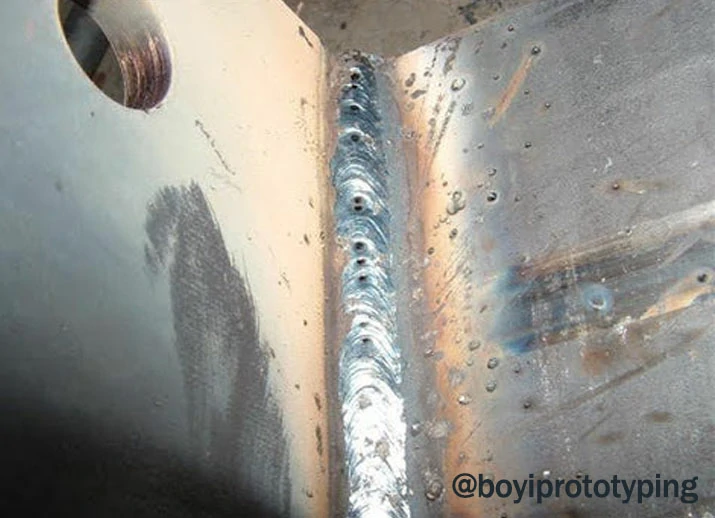
Making use of unclean or wet filler materials can present pollutants into the weld, contributing to porosity issues. To minimize these common causes of porosity, complete cleaning of base steels, correct shielding gas selection, and adherence to ideal welding criteria are vital techniques in achieving high-grade, porosity-free welds.
Impact of Porosity on Weld Top Quality

The visibility of porosity in welding can considerably compromise the architectural integrity and mechanical properties of welded joints. Porosity creates spaces within the weld steel, weakening its overall stamina and load-bearing capability.
Welds with high porosity levels tend to exhibit reduced influence stamina and decreased ability to flaw plastically prior to fracturing. Porosity can hamper the weld's capability to effectively transmit pressures, leading to premature weld failure and possible security risks in crucial frameworks.
Finest Practices for Porosity Prevention
To enhance the structural honesty and high quality of welded joints, what certain measures can be applied to reduce the event of porosity during the welding procedure? Using the right welding technique for the certain material being welded, such as readjusting the welding angle and gun setting, can further stop porosity. Regular evaluation of welds and prompt visit this page remediation of any type of concerns identified throughout the welding procedure are important techniques to prevent porosity and create high-quality welds.
Value of Correct Welding Techniques
Carrying out correct welding techniques is critical in making certain the structural integrity and high quality of bonded joints, constructing upon the foundation of effective porosity prevention procedures. Welding strategies directly impact the general stamina and sturdiness of the welded structure. One key element of appropriate welding methods is keeping the proper heat input. Excessive heat can result in use this link boosted porosity as a result of the entrapment of gases in the weld swimming pool. Alternatively, insufficient heat may result in incomplete fusion, creating potential weak points in the joint. Additionally, using the suitable welding parameters, such as voltage, existing, and travel rate, is important for attaining audio welds with very little porosity.
In addition, the option of welding process, whether it be MIG, TIG, or stick welding, should straighten with the certain requirements of the project to make certain ideal results. Correct cleansing over here and preparation of the base steel, along with selecting the ideal filler product, are also vital parts of competent welding methods. By sticking to these ideal techniques, welders can reduce the danger of porosity development and generate top quality, structurally sound welds.
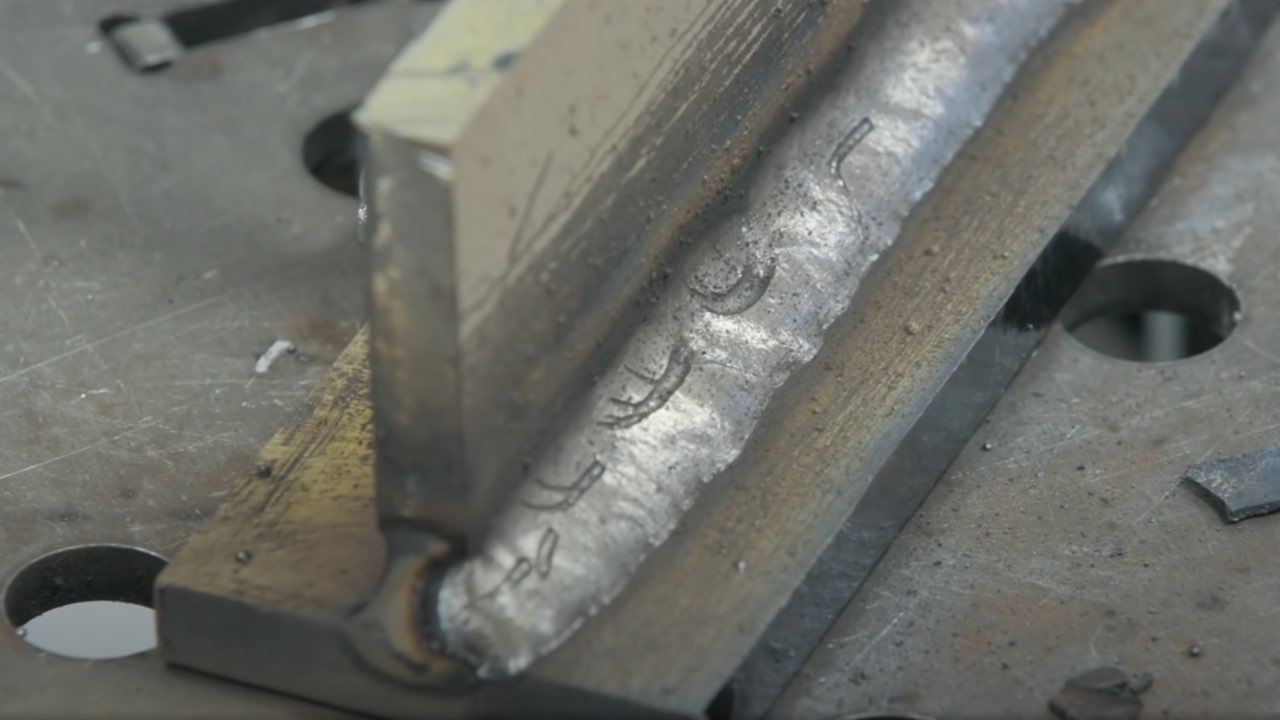
Evaluating and Quality Assurance Measures
Quality control procedures play an essential function in confirming the honesty and integrity of welded joints. Evaluating procedures are necessary to identify and prevent porosity in welding, ensuring the strength and longevity of the final item. Non-destructive testing techniques such as ultrasonic screening, radiographic screening, and aesthetic assessment are generally used to recognize possible issues like porosity. These techniques enable the assessment of weld quality without compromising the honesty of the joint. What is Porosity.
Performing pre-weld and post-weld assessments is also essential in preserving quality assurance criteria. Pre-weld assessments involve confirming the materials, tools settings, and sanitation of the workplace to stop contamination. Post-weld inspections, on the other hand, assess the final weld for any kind of flaws, consisting of porosity, and verify that it fulfills specified criteria. Implementing a detailed quality assurance strategy that consists of extensive testing procedures and inspections is extremely important to lowering porosity concerns and making sure the general quality of bonded joints.
Verdict
Finally, porosity in welding can be an usual problem that impacts the high quality of welds. By identifying the usual root causes of porosity and applying finest practices for avoidance, such as proper welding methods and screening procedures, welders can ensure high top quality and reliable welds. It is crucial to prioritize avoidance methods to lessen the occurrence of porosity and preserve the honesty of welded frameworks.
Comments on “What is Porosity in Welding: Vital Tips for Getting Flawless Welds”